Polymerization is a critical process in polymer chemistry, in which oligomers or monomers combine to form long chains or three-dimensional networks. It is one of the most important chemical processes used in the manufacture of a wide range of products, including plastics, rubber, adhesives, coatings, and more.
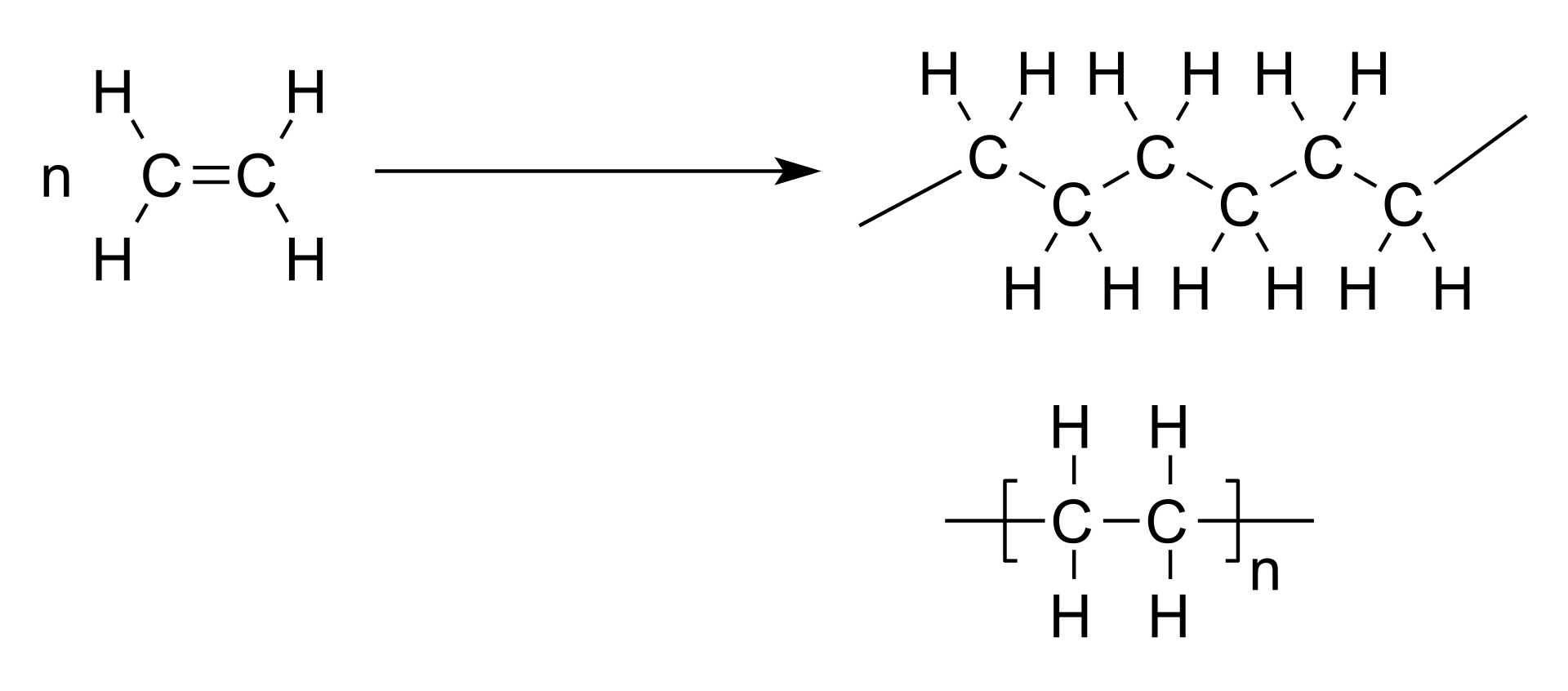
Polymers are essential materials that have unique physical, chemical, and mechanical properties. They possess high strength, stiffness, toughness, and resistance to wear, temperature, and chemicals. These properties make them ideal for a diverse range of applications, from packaging to construction to aerospace and beyond.
The polymerization process is complex and can occur through various mechanisms, including addition, condensation, and radical polymerization. Depending on the type of monomers and the reaction conditions, different polymer structures can be formed, such as linear, branched, cross-linked, and network polymers.
One of the most common forms of polymerization is addition polymerization, which involves the addition of monomer units to a growing reactive center, such as a radical or an anionic or cationic initiator. This process can occur via chain, step-growth, or living polymerization mechanisms, all of which rely on different reaction kinetics, catalysts, and initiators.
Condensation polymerization, on the other hand, involves the formation of a polymer by the elimination of small molecules, such as water, alcohol, or ammonia, from two or more monomers. This process produces polymers with ester, amide, urea, or ether linkages, which can impart specific properties, such as hydrophilicity or biodegradability, to the final product.
Radical polymerization, a type of chain-growth polymerization, is widely used in the production of commodity plastics, such as polyethylene, polystyrene, and polyvinyl chloride. This process involves the initiation of polymerization by a free radical species, followed by the chain extension and eventual termination by coupling, disproportionation, or termination agents.
Living polymerization, by contrast, is a controlled form of polymerization that allows for precise control over the polymer structure, molecular weight, and polydispersity index. This process relies on the use of specialized initiators and terminators, such as anionic or cationic agents, to manipulate the polymerization rate and prevent unwanted termination or chain transfer reactions.
Polymerization has a wide range of applications in various industries, including automotive, electronics, healthcare, and energy. It is used to produce a vast array of products, such as tires, medical implants, solar cells, and high-performance composites.
In the automotive industry, plastics produced by polymerization are used to make lightweight and fuel-efficient parts, such as bumpers, dashboards, and engine covers. In the electronics industry, polymerization is used to produce electronic-grade plastics, such as polyimides and liquid crystals, which can withstand high temperatures and harsh environments.
In healthcare, polymerization is used to produce biodegradable and biocompatible polymers, such as polylactic acid and polycaprolactone, which can be used for drug delivery and tissue engineering. In energy, polymerization is used to produce materials for energy storage, such as lithium-ion batteries, and for renewable energy, such as photovoltaic cells.
In conclusion, polymerization is a critical process in polymer chemistry that allows for the production of a vast array of materials with unique and desirable properties. The process is complex, but various mechanisms exist to control the polymer structure and molecular weight. With its numerous applications in various industries, polymerization will continue to play a vital role in modern society.